Complete knowledge of compressed air system
Compressed air system consists of air source equipment, air source purification equipment and related pipelines in a narrow sense. In a broad sense, pneumatic auxiliary components, pneumatic actuating components, pneumatic control components and vacuum components all belong to the category of compressed air system. Usually, the equipment of an air compressor station is a compressed air system in a narrow sense. The following figure shows a typical flow chart of the compressed air system:
_052.jpg)
Air source equipment (air compressor) sucks in the atmosphere, compresses the natural air into compressed air with high pressure, and removes pollutants such as moisture, oil and other impurities from the compressed air through purification equipment. The air in nature is a mixture of many gases (O, N, CO, etc.), and water vapor is one of them. Air with a certain amount of water vapor is called wet air, and air without water vapor is called dry air. The air around us is wet air, so the working medium of air compressor is naturally wet air. Although the water vapor content of humid air is relatively small, its content has a great influence on the physical properties of humid air. In the compressed air purification system, drying compressed air is one of the main contents. Under certain temperature and pressure conditions, the content of water vapor in wet air (that is, the density of water vapor) is limited. At a certain temperature, when the amount of water vapor reaches the maximum possible content, the wet air at this time is called saturated air. The wet air when the water vapor does not reach the maximum possible content is called unsaturated air. When unsaturated air becomes saturated air, liquid water drops will condense out of wet air, which is called “condensation”. Dew condensation is common, for example, the air humidity is very high in summer, and it is easy to form water droplets on the surface of tap water pipes, and water droplets will appear on the glass windows of residents in winter morning, which are all the results of dew condensation caused by the cooling of wet air under constant pressure. As mentioned above, the temperature of unsaturated air is called dew point when the temperature is reduced to reach saturation state while keeping the partial pressure of water vapor unchanged (that is, keeping the absolute water content unchanged). When the temperature drops to the dew point temperature, there is “condensation”. The dew point of wet air is not only related to temperature, but also to the moisture content in wet air. The dew point is high with large water content and low with small water content.
Dew point temperature plays an important role in compressor engineering. For example, when the outlet temperature of the air compressor is too low, the oil-gas mixture will condense in the oil-gas barrel due to the low temperature, which will make the lubricating oil contain water and affect the lubrication effect. Therefore. The outlet temperature of the air compressor must be designed to be no lower than the dew point temperature under the corresponding partial pressure. Atmospheric dew point is also the dew point temperature at atmospheric pressure. Similarly, pressure dew point refers to the dew point temperature of pressurized air. The corresponding relationship between pressure dew point and atmospheric dew point is related to the compression ratio. Under the same pressure dew point, the greater the compression ratio, the lower the corresponding atmospheric dew point. The compressed air from the air compressor is very dirty. The main pollutants are: water (liquid water droplets, water mist and gaseous water vapor), residual lubricating oil mist (atomized oil droplets and oil vapor), solid impurities (rust mud, metal powder, rubber powder, tar particles and filter materials, sealing materials, etc.), harmful chemical impurities and other impurities. Deteriorated lubricating oil will deteriorate rubber, plastic and sealing materials, cause valve action failure and pollute products. Moisture and dust will cause rust and corrosion of metal devices and pipelines, cause moving parts to be stuck or worn, make pneumatic components malfunction or leak, and moisture and dust will also block throttle holes or filter screens. In cold areas, pipelines will freeze or crack after moisture freezes. Because of the poor air quality, the reliability and service life of pneumatic system are greatly reduced, and the losses caused by it often greatly exceed the cost and maintenance cost of air source treatment device, so it is absolutely necessary to choose air source treatment system correctly.
What is the main source of moisture in compressed air? The main source of moisture in compressed air is water vapor sucked by air compressor together with air. After wet air enters the air compressor, a large amount of water vapor is squeezed into liquid water during the compression process, which will greatly reduce the relative humidity of compressed air at the outlet of the air compressor. If the system pressure is 0.7MPa and the relative humidity of the inhaled air is 80%, the compressed air output from the air compressor is saturated under pressure, but if it is converted to the atmospheric pressure before compression, its relative humidity is only 6~10%. That is to say, the water content of compressed air has been greatly reduced. However, with the gradual decrease of temperature in gas pipelines and gas equipment, a large amount of liquid water will continue to condense in compressed air. How is oil pollution in compressed air caused? Lubricating oil of air compressor, oil vapor and suspended oil droplets in ambient air and lubricating oil of pneumatic components in the system are the main sources of oil pollution in compressed air. At present, except centrifugal and diaphragm air compressors, almost all air compressors (including all kinds of oil-free lubricated air compressors) will bring dirty oil (oil drops, oil mist, oil vapor and carbonized fission products) into the gas pipeline to some extent. The high temperature of the compression chamber of the air compressor will cause about 5%~6% of the oil to vaporize, crack and oxidize, which will accumulate in the inner wall of the air compressor pipeline in the form of carbon and lacquer film, and the light fraction will be brought into the system by compressed air in the form of steam and tiny suspended matter. In a word, all oils and lubricating materials mixed in the compressed air can be regarded as oil-contaminated materials for systems that do not need to add lubricating materials when working. For the system that needs to add lubricating materials in the work, all antirust paint and compressor oil contained in compressed air are considered as oil pollution impurities.
How do solid impurities get into compressed air? The sources of solid impurities in compressed air mainly include: (1) There are various impurities with different particle sizes in the surrounding atmosphere. Even if an air filter is installed at the air inlet of the air compressor, usually “aerosol” impurities below 5μm can enter the air compressor with the inhaled air, and mix with oil and water to enter the exhaust pipeline during compression. (2) When the air compressor is working, the parts rub and collide with each other, the seals are aging and falling off, and the lubricating oil is carbonized and fissioned at high temperature, which can be said that solid particles such as metal particles, rubber dust and carbonaceous fission are brought into the gas pipeline. What is the air source equipment? What are there? The source equipment is the compressed air generator-air compressor (air compressor). There are many types of air compressors, such as piston type, centrifugal type, screw type, sliding type and scroll type.
_022.jpg)
The compressed air output from the air compressor contains a lot of pollutants such as moisture, oil and dust, so it is necessary to use purification equipment to remove these pollutants properly to avoid their harm to the normal work of the pneumatic system. Air source purification equipment is a general term for many equipments and devices. Gas source purification equipment is also often called post-treatment equipment in the industry, which usually refers to gas storage tanks, dryers, filters and so on. ● Gas storage tank The function of the gas storage tank is to eliminate pressure pulsation, further separate water and oil from compressed air by adiabatic expansion and natural cooling, and store a certain amount of gas. On the one hand, it can alleviate the contradiction that the gas consumption is greater than the output gas of the air compressor in a short time, on the other hand, it can maintain the gas supply for a short time when the air compressor fails or loses power, so as to ensure the safety of pneumatic equipment.
The compressed air output from the air compressor contains a lot of pollutants such as moisture, oil and dust, so it is necessary to use purification equipment to remove these pollutants properly to avoid their harm to the normal work of the pneumatic system. Air source purification equipment is a general term for many equipments and devices. Gas source purification equipment is also often called post-treatment equipment in the industry, which usually refers to gas storage tanks, dryers, filters and so on. ● Gas storage tank The function of the gas storage tank is to eliminate pressure pulsation, further separate water and oil from compressed air by adiabatic expansion and natural cooling, and store a certain amount of gas. On the one hand, it can alleviate the contradiction that the gas consumption is greater than the output gas of the air compressor in a short time, on the other hand, it can maintain the gas supply for a short time when the air compressor fails or loses power, so as to ensure the safety of pneumatic equipment.
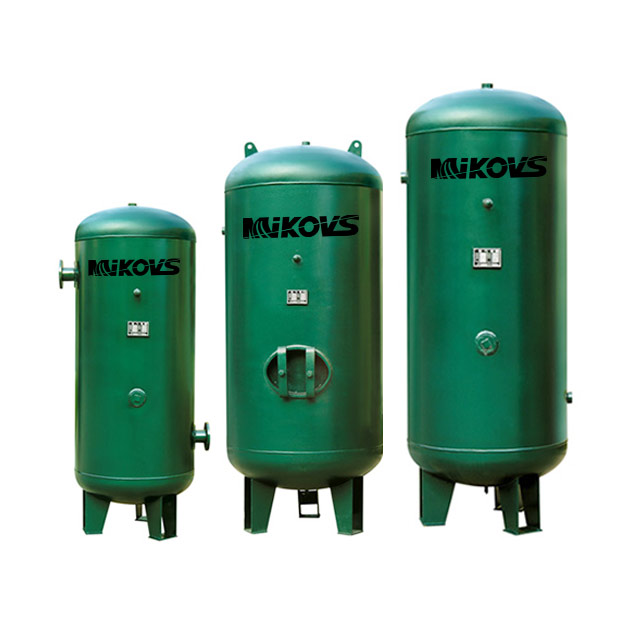
● Dryer Compressed air dryer, as its name implies, is a kind of water removal equipment for compressed air. There are two commonly used types: freeze dryer and adsorption dryer, as well as deliquescence dryer and polymer diaphragm dryer. Freeze dryer is the most commonly used compressed air dehydration equipment, which is usually used in situations where the quality of general gas sources is required. Freeze-dryer is to use the characteristic that the partial pressure of water vapor in compressed air is determined by the temperature of compressed air to cool and dehydrate. Compressed air freeze dryer is generally referred to as “cold dryer” in the industry. Its main function is to reduce the water content in compressed air, that is, to reduce the dew point temperature of compressed air. In general industrial compressed air system, it is one of the necessary equipment for compressed air drying and purification (also known as post-treatment).
1 basic principles Compressed air can be pressurized, cooled, absorbed and other methods to achieve the purpose of removing water vapor. Freeze-dryer is the method of applying cooling. As we know, the air compressed by air compressor contains all kinds of gases and water vapor, so it is all wet air. The moisture content of humid air is inversely proportional to the pressure as a whole, that is, the higher the pressure, the less the moisture content. After the air pressure increases, the water vapor in the air that exceeds the possible content will condense into water (that is, the compressed air volume becomes smaller and cannot accommodate the original water vapor). This is relative to the original air when inhaled, the moisture content is smaller (here refers to the fact that this part of compressed air is restored to an uncompressed state). However, the exhaust of air compressor is still compressed air, and its water vapor content is at the maximum possible value, that is, it is in a critical state of gas and liquid. At this time, the compressed air is called saturated state, so as long as it is slightly pressurized, water vapor will change from gas to liquid immediately, that is, water will condense out. Suppose that air is a wet sponge that absorbs water, and its moisture content is the inhaled moisture. If some water is squeezed out of the sponge by force, the moisture content of this sponge is relatively reduced. If you let the sponge recover, it will naturally be drier than the original sponge. This also achieves the purpose of dehydration and drying by pressurizing. If no force is applied after reaching a certain strength in the process of squeezing the sponge, the water will stop being squeezed out, which is the saturation state. Continue to increase the intensity of extrusion, there is still water flowing out. Therefore, the air compressor itself has the function of removing water, and the method used is pressurization. However, this is not the purpose of the air compressor, but a “nuisance”. Why not use “pressurization” as a means to remove water from compressed air? This is mainly because of economy, increasing the pressure by 1 kg. It is quite uneconomical to consume about 7% energy. But “cooling” to remove water is relatively economical, and the freezing dryer uses the similar principle as air conditioning dehumidification to achieve its goal. Because the density of saturated water vapor is limited, in the range of aerodynamic pressure (2MPa), it can be considered that the density of water vapor in saturated air depends only on the temperature, but has nothing to do with air pressure. The higher the temperature, the greater the density of water vapor in saturated air, and the more water. On the contrary, the lower the temperature, the less water (this can be understood from common sense of life, dry and cold in winter and humid and hot in summer). The compressed air is cooled to the lowest possible temperature, so that the density of water vapor contained in it becomes smaller, and “condensation” is formed, and the small water droplets formed by these condensation are gathered and discharged, thus achieving the purpose of removing water from the compressed air. Because it involves the process of condensation and condensation into water, the temperature should not be lower than the “freezing point”, otherwise the freezing phenomenon will not effectively drain water. Usually, the nominal “pressure dew point temperature” of freeze dryer is mostly 2~10℃. For example, the “pressure dew point” of 0.7MPa at 10℃ is converted into “atmospheric dew point” of -16℃. It can be understood that when the compressed air is used in an environment not lower than -16℃, there will be no liquid water when it is exhausted to the atmosphere. All water removal methods of compressed air are only relatively dry, meeting a certain required dryness. Absolute moisture removal is impossible, and it is very uneconomical to pursue dryness beyond the use demand. 2 working principle The compressed air freezing dryer can reduce the moisture content of compressed air by cooling the compressed air and condensing the water vapor in the compressed air into droplets. The condensed liquid drops are discharged from the machine through the automatic drainage system. As long as the ambient temperature of the pipeline downstream of the dryer outlet is not lower than the dew point temperature of the evaporator outlet, the phenomenon of secondary condensation will not occur.
Compressed air process: The compressed air enters the air heat exchanger (preheater) [1] to reduce the temperature of the high-temperature compressed air initially, and then enters the Freon/air heat exchanger (evaporator) [2], where the compressed air is extremely cooled, and the temperature is greatly reduced to the dew point temperature. The separated liquid water and the compressed air are separated in the water separator [3], and the separated water is discharged out of the machine by an automatic drainage device. The compressed air exchanges heat with the low-temperature refrigerant in the evaporator [2], and the temperature of the compressed air at this time is very low, approximately equal to the dew point temperature of 2~10℃. If there is no special requirement (that is, there is no low temperature requirement for compressed air), usually the compressed air will return to the air heat exchanger (preheater) [1] to exchange heat with the high temperature compressed air that has just entered the cold dryer. The purpose of this is: (1) effectively use the “waste cold” of the dried compressed air to pre-cool the high-temperature compressed air just entering the cold dryer, so as to reduce the refrigeration load of the cold dryer; (2) to prevent secondary problems such as condensation, dripping, rust, etc. outside the back-end pipeline caused by low-temperature compressed air after drying. Refrigeration process: Refrigerant Freon enters the compressor [4], and after compression, the pressure increases (the temperature also increases). When it is slightly higher than the pressure in the condenser, the high-pressure refrigerant vapor is discharged into the condenser [6]. In the condenser, refrigerant vapor with higher temperature and pressure exchanges heat with air (air cooling) or cooling water (water cooling) with lower temperature, thereby condensing refrigerant Freon into liquid state. At this time, the liquid refrigerant is depressurized (cooled) by the capillary/expansion valve [8] and then enters the Freon/air heat exchanger (evaporator) [2], where it absorbs the heat of compressed air and gasifies. The cooled object-compressed air is cooled, and the vaporized refrigerant vapor is sucked away by the compressor to start the next cycle.
Refrigerant in the system completes a cycle through four processes: compression, condensation, expansion (throttling) and evaporation. Through continuous refrigeration cycle, the purpose of freezing compressed air is realized. 4 Function of each component Air heat exchanger In order to prevent condensed water from forming on the outer wall of the external pipeline, the air after freeze-drying leaves the evaporator and exchanges heat with the compressed air with high temperature and damp heat in the air heat exchanger again. At the same time, the temperature of air entering the evaporator is greatly reduced. heat exchange The refrigerant absorbs heat and expands in the evaporator, changing from liquid to gas, and the compressed air exchanges heat to cool down, so that the water vapor in the compressed air changes from gas to liquid. water separator The separated liquid water is separated from the compressed air in the water separator. The higher the separation efficiency of the water separator, the smaller the proportion of liquid water re-volatilizing into the compressed air, and the lower the pressure dew point of the compressed air. compressor Gaseous refrigerant enters the refrigeration compressor and is compressed to become high temperature and high pressure gaseous refrigerant. by-pass valve If the temperature of the separated liquid water drops below freezing point, the condensed ice will cause ice blockage. By-pass valve can control the refrigeration temperature and the pressure dew point at a stable temperature (1~6℃). condenser The condenser lowers the temperature of the refrigerant, and the refrigerant changes from a high-temperature gaseous state to a low-temperature liquid state. filter The filter effectively filters the impurities of the refrigerant. Capillary/expansion valve After passing through the capillary/expansion valve, the refrigerant expands in volume and decreases in temperature, and becomes a low-temperature and low-pressure liquid. gas-liquid separator As liquid refrigerant enters the compressor, it may produce liquid hammer phenomenon, which may lead to the damage of the refrigeration compressor. Only gaseous refrigerant can enter the refrigeration compressor through the refrigerant gas-liquid separator. Automatic drainer The automatic drainer regularly discharges the liquid water accumulated at the bottom of the separator outside the machine. Freeze dryer has the advantages of compact structure, convenient use and maintenance, low maintenance cost, etc., and is suitable for occasions where the dew point temperature of compressed air pressure is not too low (above 0℃). Adsorption dryer uses desiccant to dehumidify and dry the forced compressed air. Regenerative adsorption dryer is often used in daily life.
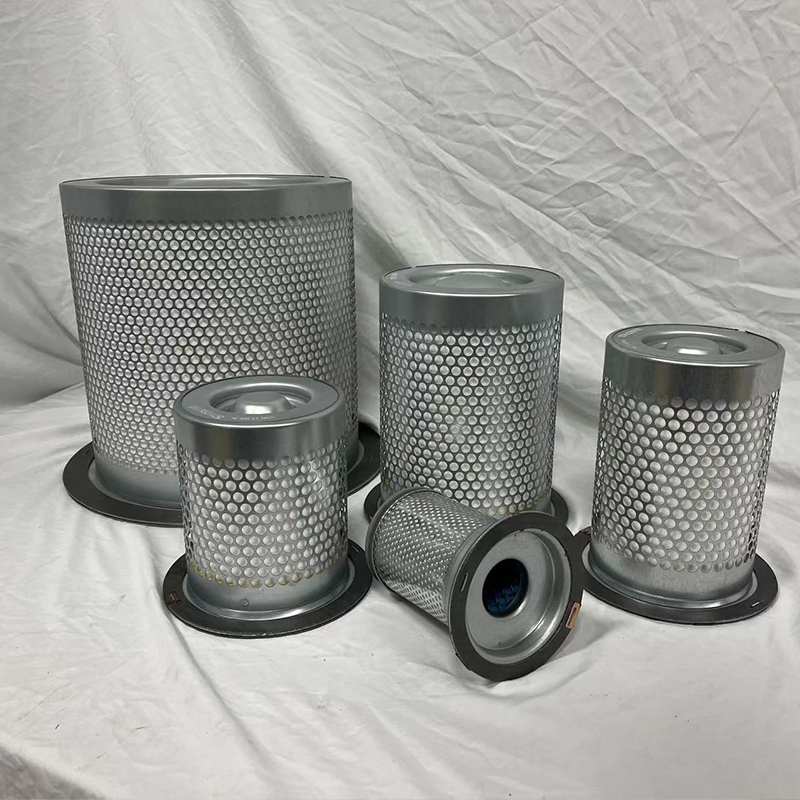
● Filter Filters are divided into main pipeline filter, gas-water separator, activated carbon deodorizing filter, steam sterilization filter, etc. Their functions are to remove oil, dust, moisture and other impurities in the air to obtain clean compressed air. Source: compressor technology Disclaimer: This article is reproduced from the network, and the content of the article is only for learning and communication. The air compressor network is neutral to the views in the article. The copyright of the article belongs to the original author and the platform. If there is any infringement, please contact to delete it.